Plastic extrusion for efficient, flexible manufacturing solutions
Plastic extrusion for efficient, flexible manufacturing solutions
Blog Article
A Comprehensive Guide to the Process and Benefits of Plastic Extrusion
In the large realm of manufacturing, plastic extrusion emerges as a crucial and very efficient procedure. Translating raw plastic into continuous profiles, it provides to a wide variety of markets with its impressive flexibility.
Comprehending the Essentials of Plastic Extrusion
While it might show up complicated initially look, the process of plastic extrusion is essentially straightforward - plastic extrusion. It is a high-volume production technique in which raw plastic is melted and shaped into a constant account. The procedure starts with the feeding of plastic product, in the type of powders, granules, or pellets, right into a warmed barrel. The plastic is then thawed making use of a mix of warm and shear, applied by a revolving screw. As soon as the molten plastic gets to the end of the barrel, it is compelled via a tiny opening referred to as a die, forming it right into a wanted type. The shaped plastic is then cooled, solidified, and reduced right into wanted sizes, completing the process.
The Technical Refine of Plastic Extrusion Explained

Kinds of Plastic Suitable for Extrusion
The selection of the appropriate kind of plastic is a critical facet of the extrusion process. Numerous plastics supply one-of-a-kind properties, making them extra fit to specific applications. Understanding these plastic kinds can dramatically enhance the extrusion procedure.
Comparing Plastic Extrusion to Various Other Plastic Forming Techniques
Understanding the kinds of plastic suitable for extrusion leads the way for a broader conversation on how plastic extrusion compares to various other plastic forming approaches. These include shot molding, strike molding, and thermoforming. Each approach has its distinct usages and benefits. Injection molding, for circumstances, is outstanding for creating elaborate parts, while impact molding is best for hollow objects like containers. Thermoforming excels at creating shallow or huge parts. Nevertheless, plastic extrusion is unrivaled when it concerns creating continuous accounts, such as gaskets, seals, and pipelines. It also permits a constant cross-section along the size of the product. Therefore, the option of approach mostly depends on the end-product needs and requirements.
Key Advantages of Plastic Extrusion in Manufacturing
In the realm of manufacturing, plastic extrusion offers several substantial benefits. One notable benefit is the cost-effectiveness of the process, that makes it a financially enticing manufacturing technique. Furthermore, this strategy provides exceptional item flexibility and boosted production speed, therefore boosting general production effectiveness.
Cost-Effective Production Approach
Plastic extrusion jumps to the center as an economical production method in production. This procedure attracts attention for its ability to create high quantities of material quickly and successfully, offering manufacturers with significant financial savings. The primary price advantage is the ability to use less costly raw materials. Extrusion uses thermoplastic materials, which are much less costly contrasted to porcelains or metals. Even more, the extrusion process itself is reasonably simple, lowering labor expenses. Additionally, plastic extrusion requires much less energy than traditional production techniques, adding to reduced operational costs. The procedure likewise decreases waste, as any faulty or excess products can be recycled and reused, providing an additional layer of cost-effectiveness. On the whole, the economic benefits make plastic extrusion a highly appealing alternative in the manufacturing industry.
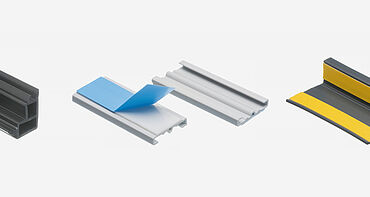
Superior Item Versatility
Beyond the cost-effectiveness of plastic extrusion, one more substantial benefit in producing lies in its premium product adaptability. This procedure enables the development of a broad variety of products with differing forms, dimensions, and layouts, from easy plastic sheets to intricate profiles. The versatility is connected to the extrusion die, which can be customized to generate the wanted product style. This makes plastic extrusion an optimal option for markets that require personalized plastic elements, such as vehicle, construction, and product packaging. The ability to produce diverse products is not just useful in meeting details market demands but likewise in allowing makers to check out brand-new product with very little resources financial investment. In significance, plastic extrusion's product adaptability cultivates technology while improving functional efficiency.
Enhanced Production Rate
A significant benefit of plastic extrusion depends on its boosted production speed. This production process enables high-volume production in a relatively brief time period. It can producing long, continuous plastic profiles, which substantially reduces the production time. This high-speed production is particularly beneficial in markets where big quantities of plastic parts are needed within tight due dates. Few other production procedures can match the rate of plastic extrusion. Furthermore, visit site the capability to maintain constant high-speed manufacturing without compromising product high quality establishes plastic extrusion apart from various other methods. The enhanced manufacturing speed, as a result, not just allows producers to meet high-demand orders however additionally adds to boosted performance and cost-effectiveness. This advantageous attribute of plastic extrusion has actually made it a favored choice in countless industries.
Real-world Applications and Influences of Plastic Extrusion
In the realm of production, the strategy of plastic extrusion holds extensive relevance. This procedure is extensively utilized in the production of a range of products, such as plastic tubes, home window structures, and climate stripping. Because of this, it significantly influences fields like building, product packaging, and automotive industries. Its influence expands to daily things, from plastic bags to toothbrushes and disposable flatware. The financial benefit of plastic extrusion, primarily its economical and high-volume result, has actually revolutionized production. The ecological influence of plastic waste continues to be a problem. The market is constantly striving for advancements in recyclable and eco-friendly products, showing a future where the advantages his comment is here of plastic extrusion can be kept without endangering environmental sustainability.
Final thought
To conclude, plastic extrusion is a efficient and highly effective approach of changing basic materials into diverse items. It supplies many benefits over various other plastic forming approaches, consisting of cost-effectiveness, high outcome, marginal waste, and design versatility. Its impact is exceptionally really felt in different markets such as building, automobile, and customer products, making it a pivotal process in today's manufacturing landscape.
Delving deeper into the technical process of plastic extrusion, it starts with the choice of the proper plastic product. Once cooled, the plastic is reduced into the needed lengths or injury onto reels if the product is a plastic film or sheet - plastic extrusion. Comparing Plastic Extrusion to Various Other Plastic Forming Approaches
Comprehending the types of plastic appropriate for extrusion leads the method for a more click to read more comprehensive discussion on how plastic extrusion piles up against various other plastic forming techniques. Few other manufacturing procedures can match the rate of plastic extrusion.
Report this page